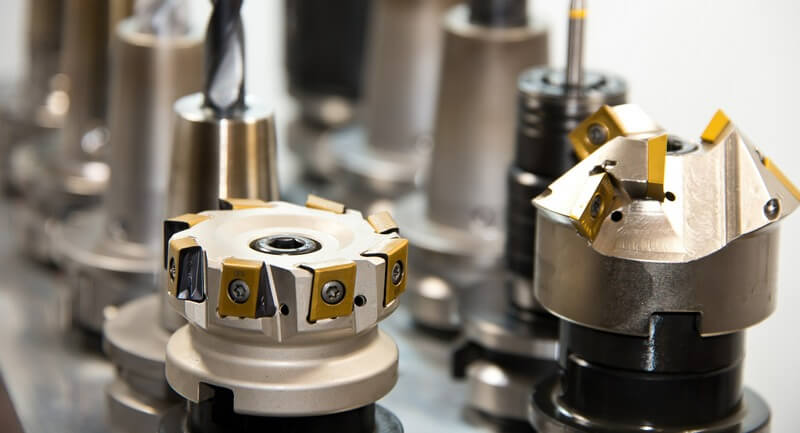
One of MGM Manufacturing’s greatest strengths is offering unique solutions to manufacturing challenges our valued customers’ encounter in procuring their complex metal fabricated and machined parts. We at MGM take great pride in helping our clientele save money on their projects when it comes to manufacturing costs, increase their productivity of parts and meet their tight delivery requirements by thinking outside the box and offering special answers to their most challenging manufacturing parts requirements!
With MGM Manufacturing not only do you have a seasoned manufacturing supplier with the extensive expertise for producing complex CNC machined and fabricated parts, but you have a true partner working hand-in-hand with your in-house design and production team to find solutions to your manufacturing difficulties.
The following are just a few examples of some manufacturing challenges our customers have encountered over the years and some of our creative solutions to their “problem child” projects and components…
Customer #1: FAA Repair Station
Type of Parts: Machined Aluminum Bracket
Customer Problems:
Our customer who was a Certified FAA Repair Station was encountering problems with replacing unique Aluminum “Bracket” parts used in aircraft seats they had to repair for an old commercial freight aircraft. The OEM manufacturer of these parts had gone out of business and the parts the repair station had produced in their own in-house machine shop were constantly cracking in-flight after a short period of time. This constant procurement of parts was costly and inconvenient to our customer and to their respective customer as well.
MGM Manufacturing’s Solutions:
MGM’s skilled team of machinists recommended and machined this customer’s part from a stronger alternative “Aluminum 7075” aircraft alloy instead of “Aluminum 6061” alloy that they were originally utilizing. In addition, MGM recommended that this part be heat treated after machining to further strengthen it and prevent future in-flight cracking. As a result, the new Brackets produced by MGM Manufacturing did not crack and did not have to be replaced as frequently on the aircraft.
Customer #2: Energy/Power Plant
Type of Parts: Machined Titanium Housing
Customer Problems:
Our customer who was a power plant in the U.S. faced growing difficulties in having their existing supplier provide a critical machined Magnesium castings to them with a timely delivery. Likewise they faced ever increasing costs for these castings that were undesirable.
MGM Manufacturing’s Solutions:
The MGM team recommended firm and fixed pricing to procure their entire yearly requirement of the parts from solid blocks of Titaniumalloy instead of the costly Magnesium castings. Titanium alloy is both a strong and a light weight alloy which does not have the manufacturing headaches of a Magnesium casting. By machining the parts from solid Titanium block, the customer was also able to get lower pricing because machining of solid Titanium block is less volatile and less costly than have a Magnesium casting made and then having it machined.
Additionally MGM machined the entire annual requirement of parts for our customer in two runs. Then we placed the customers’ parts in our inventory and shipped them in a KanBan system per their quarterly requirements. This resulted in zero delivery delays for these critical parts and stable pricing for the parts to meet their budgetary requirements.
Customer #3: Industrial Machinery OEM
Type of Parts: 5-AxisMachined Part from 15-5PH Stainless Steel
Customer Problems:
Our customer was machining one of their critical complex 5-Axis parts for their final machinery product at their own facility at a very high cost. This high cost was preventing them from selling a higher volume of their final machinery equipment to potential new customers. Another major problem our customer encountered was the substantial distortion of the parts that occurred during their machining operations.
MGM Manufacturing’s Solutions:
The team at MGM developed special tooling to reduce the machining cycle time for these complex parts by half. More importantly, our talented crew of seasoned machinists reduced the speed and feed of the machining on these parts to prevent the distortion generated by these parts. These two critical steps enabled MGM Manufacturing to continuously produce less costly parts, with zero distortions and no other quality deficiencies. As a result our customer within a short time period was able to successfully increase production of their final equipment product and increase their sales of the product by two fold!